Aspheres
Amazing Range of Aspheric Capabilities!
Aspheric Lenses
Aspheric lenses allow optical engineers to correct aberrations using fewer components than spherical optics since the former provides greater aberration correction than multiple surfaces of the latter. Given this, many spherical lenses may be replaced with smaller amounts of aspheric ones to achieve comparable or superior optical outcomes while reducing system size, simplifying the manufacturing procedure, and producing imaging lenses that are less expensive and outperform traditional spherical component assemblies.
Download Our Latest Brochure On Aspherical Lenses
Single Point Diamond Turning (SPDT)
Asphera’s Single Point Diamond Turning (SPDT) offers the highest precision for manufacturing complex aspherical shapes. SPDT is mostly known for fabricating micro-optics with features down to 1 micron in size. SPDT replaces the standard lathe with a diamond tip bit to achieve surface roughness of only a few nanometers.
Advantages: Offers the highest lens shape accuracy without any high tooling costs - only tooling required is the diamond bit
Disadvantages: High reject rate, long lead times, not suitable for mass production
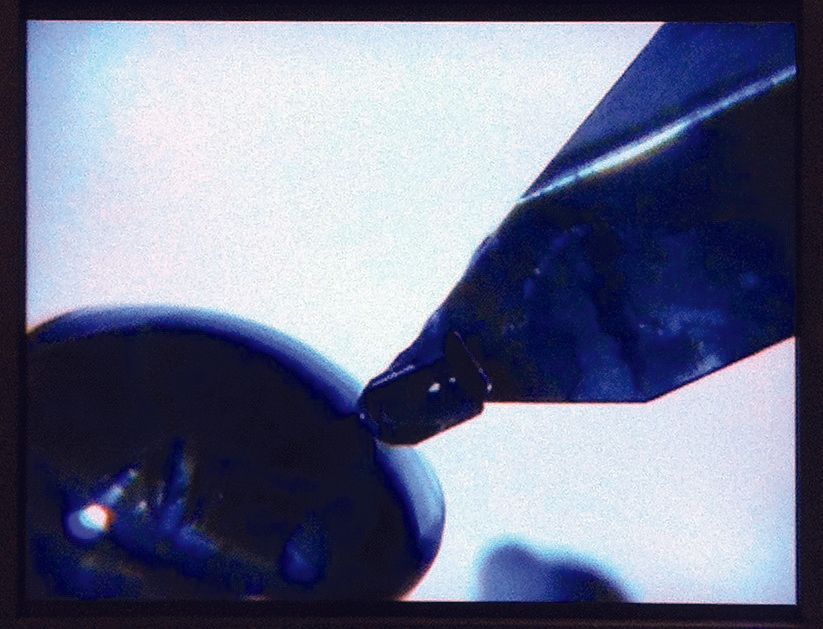
Materials:
Germanium, Silicon, Calcium Fluoride, Zinc Selenide, Zinc SUlfide, Multi-spectral Zinc Sulfide, Chalcogenide glass (Gallium Arsenide
Diameter:
5-300 mm
Surface ACcuracy
PV=0.07μm
Surface Roughness
0.9nm
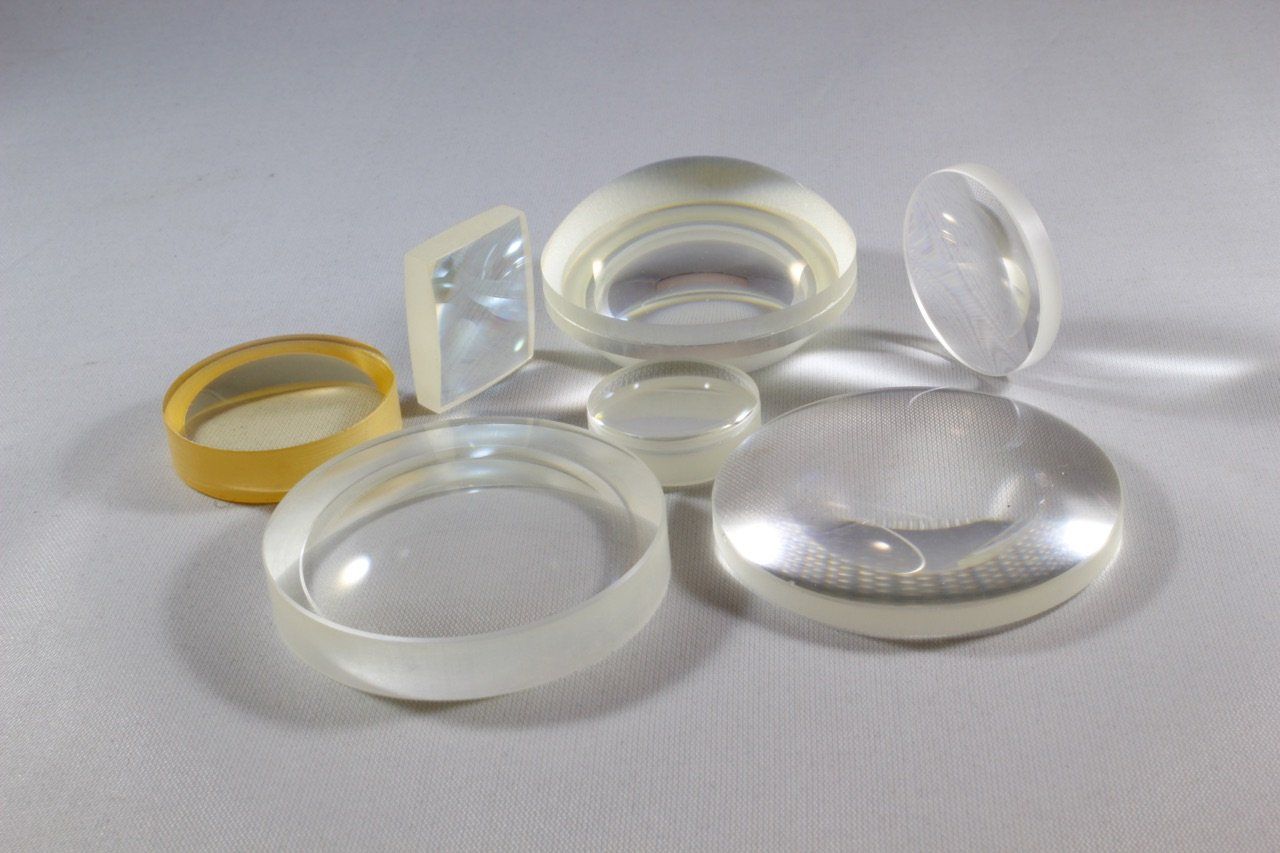
Glass Materials:
Schott, Ohara, CDGM
UV Fused Silica Material:
Hereaus, Corning
Diameter:
4-750 mm
Thickness:
2-80mm
Dimensional Tolerance
+0/-0.01mm
Scratch-dig
10-5
Irregularity (p-v)
1 fringe-0.3μm
CNC Polished Glass Aspheres
Computer Numerical Control (CNC) polishing is the most efficient method of asphere fabrication. it relies on the traditional optics technique of pushing one lens at a time on a computer-controlled platform that adjusts the shape on a spindle, spinning the lens at a high speed to reach the desired surface profile. Our 5 axis machine is 3-5x faster than traditional CNC polished aspheres. This technique is chosen for its high precision, reliability, and capabilities with wide ranges of size and materials. For volume cost and speed, it is best for diameters between 30-50mm. When diameters below 10mm are needed, it is best to consider this method's limitations of cost efficiency and volume processing.
Advantages: Better Surface Quality, complex shapes, large diameter capabilities, wide selection of materials.
Disadvantages: Volume capabilities, cost efficiency, small diameter capabilities
Precision Molded Aspheres
The ideal asphere is a ground prototype design that is machined and then transferred to a mold for production. Precision Glass Molding (PGM) is a fabricating a mold from a thermally and physically durable material created with an optical quality surface profile that accounts for shrinkage as the glass cools. PMG is the best choice for high volume production runs with with little compromise in quality compared to SPDT and polishing. The mold can be made with multiple cavities to produce many lenses quickly and inexpensively. However, PGM is not often the choice of many designers because material selections are limited to glasses with low transformation temperature of <550°C. Another aspect of PGM is that the index of refraction drops by around 0.002-0.005 of its original value and must be taken into consideration.
Advantages: Better RMS surface figure than CNC machined spheres, quick and inexpensive, small diameters down to 1mm
Disadvantages: Limited choice of materials, size limitations for large diameters, best achievable surface quality is 40/20
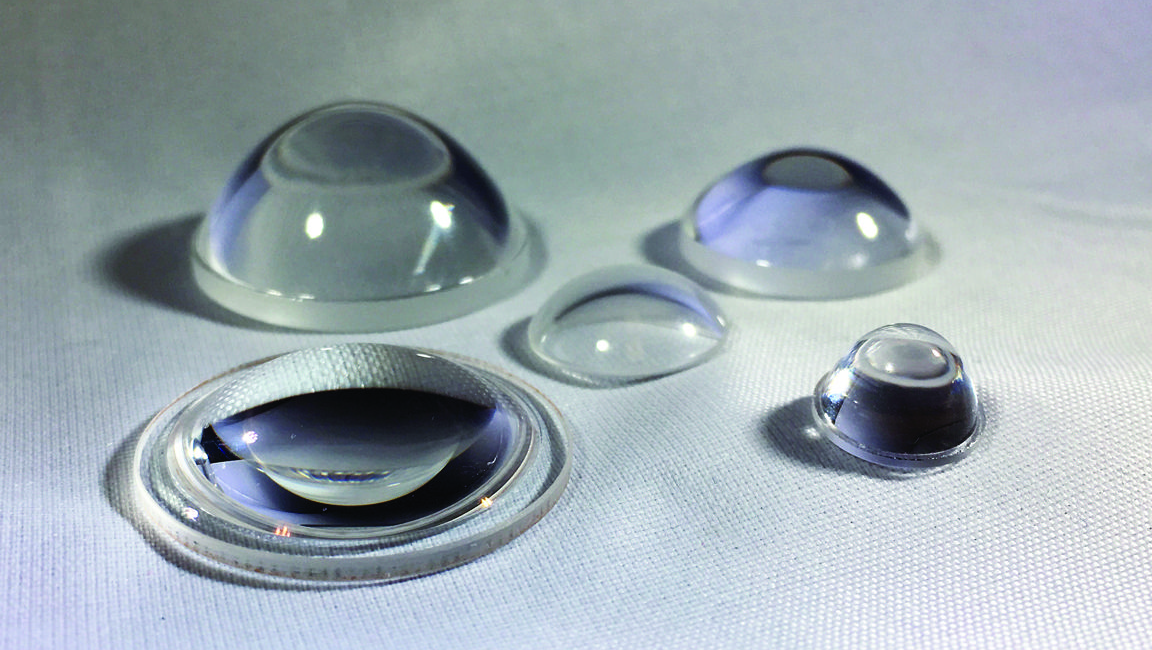
Materials:
Glasses with Ti contents <1%
Fused Silica: Corning C0550
Diameter:
1-90mm
Diameter Tolerance
±0.015mm
Surface Quality
40/20
Focal Length Tolerance
±1%